Молодые ученые Трубной Металлургической Компании (ТМК) стали лауреатами премии правительства РФ в области науки и техники. Они изобрели и внедрили в производство уникальную технологию цифровых двойников.
Разработка напоминает компьютерную игру, которая позволяет моделировать процессы производства труб для нефтегазовой отрасли на непрерывных раскатных, извлекательно-калибровочных и редукционных станах. Проигрывая в виртуальном пространстве различные сценарии, специалисты выбирают оптимальные настройки оборудования и получают продукт с максимально точными характеристиками при минимальном расходе материала.
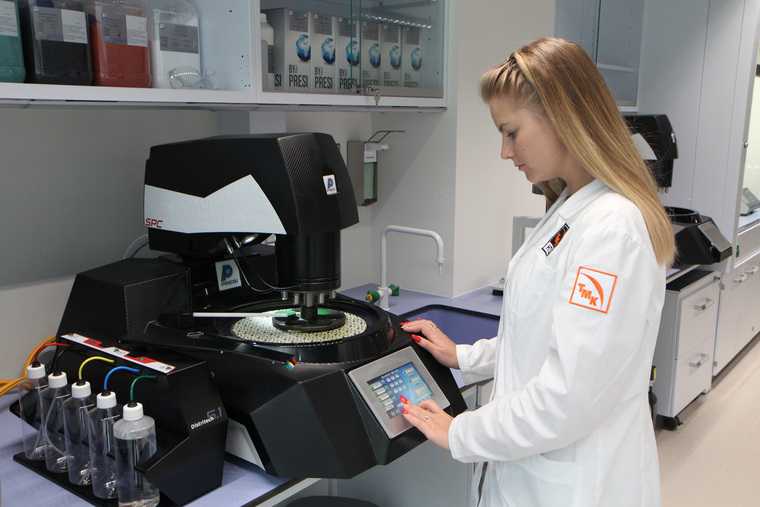
Благодаря технологии цифрового двойника, на предприятиях компании увеличилась доля продукции с геометрическими параметрами повышенной точности. Также компьютерный помощник помог освоить процесс выпуска высокоточных труб для подводных трубопроводов и труб из новых марок стали — более высокого качества и прочности. Что важно, независимо от вида продукции, цифровой двойник помогает добиться постоянного результата на протяжении всей прокатной кампании.
«Допустим, по действующей технологии мы производим трубу с погрешностью по толщине стенки например плюс-минус 8%, чтобы улучшить этот показатель и обеспечить его постоянство на протяжении всей прокатной кампании, и учесть то множество факторов, которые оказывают влияние на процесс создания высокотехнологичной продукции, необходима такая система которая позволяет осуществлять непрерывный анализ технологии и выдачу соответствующих рекомендаций и корректировок. Технология цифрового двойника путем анализа данных, регистрируемых на стане, позволяет это делать в оперативном режиме и выдавать оптимальные параметры по управлению технологическим процессом. Тем самым мы обеспечиваем необходимые требования к выпускаемой продукции, предъявляемые заказчиком», — прокомментировал один из лауреатов премии — заведующий лабораторией Научно-технического центра (НТЦ) ТМК в «Сколково» Евгений Шкуратов.
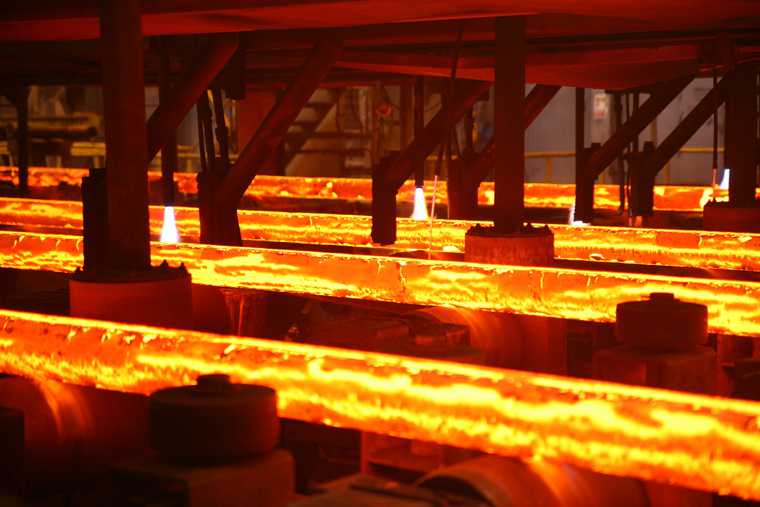
По его словам, вопрос о создании цифрового двойника встал перед командой ТМК еще в 2013—2014 годах. На предприятиях провели глобальную модернизацию мощностей, были закуплены новейшие прокатные агрегаты. И чтобы оптимизировать технологию работы с ними, каждый раз приходилось проходить несколько этапов: сначала проводить тщательный теоретический анализ, затем выполнять компьютерное моделирование, далее — опробовать новую технологию на экспериментальном прокатном стане, и только после этого она внедрялась в производство.
«Как вы понимаете, все эти этапы с точки зрения времени, сил, достаточно затратны. А те математические модели, те системы ограничений, которые мы разработали, позволяют совершенствовать технологию значительно быстрее. Нам уже не требуется столько этапов, мы буквально за считанные минуты и часы можем оптимизировать технологию для получения нужных характеристик продукта», — отметил Шкуратов.
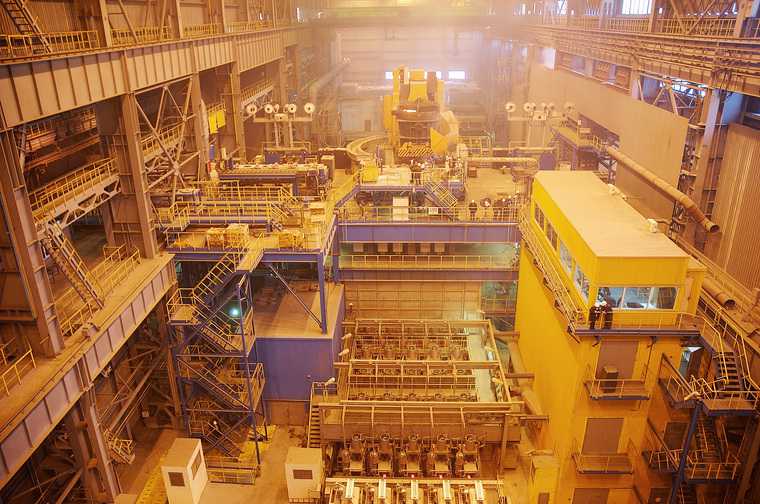
К 2018 году команда ТМК разработала «ядро» — комплекс математических моделей, которые и легли в основу создания цифрового двойника. Далее, к концу 2018 — началу 2019 года, технологию обкатали на Северском трубном заводе (Полевской), входящем в ТМК: стан, который эксплуатируется там, регистрирует большие объемы данных, поэтому начать с него было проще всего. Благодаря цифровому двойнику, был разработан новый принцип построения калибровки валков чистовых калибров. На основе него уже прокатано более 30 тысяч тонн труб повышенной точности. Также проведены работы по оптимизации скорости перемещения оправок непрерывного стана, что позволило сократить её длину и экономить на закупках дорогостоящего инструмента.
Сейчас технология цифрового двойника обкатывается и для Волжского трубного завода (ВТЗ), также входящего в ТМК. Там проходят различные испытания по освоению новых видов продукции, в частности, из высоколегированных марок стали (с улучшенными характеристиками). Затем эта продукция будет прокатана на стане.
Следующий шаг в масштабировании технологии — Таганрогский металлургический завод (ТАГМЕТ). «Цифровой двойник, разработанный для Северского трубного завода, в полной мере не может быть перенесен в Таганрог. Хоть оборудование и похоже, но все равно имеет свои специфические особенности», — рассказал Шкуратов.
Релиз программы ТАГМЕТа намечен на конец года. В перспективе ученые планируют использовать разработку не только для управления прокатными станами, но и на всех участках производства.
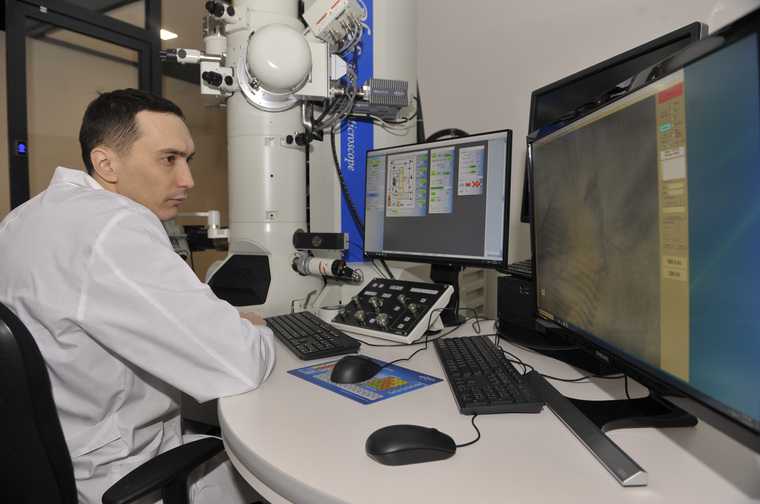
Следует отметить, что разработка технологии цифрового двойника велась сначала на базе Российского научно-исследовательского института трубной промышленности (РосНИТИ) в Челябинске, позже технология совершенствовалась на базе НТЦ ТМК в «Сколково». Последний был введен в эксплуатацию в конце 2019 года. Он оснащен высокоточным исследовательским оборудованием, а также испытательными стендами, которые позволяют растягивать, сжимать, изгибать трубы с приложением наружного и внутреннего давления и созданием экстремальных температур. Это уникальный лабораторно-исследовательский комплекс для нашей страны, а в мире подобных центров насчитывается всего пять.
Автор: Елена Усенова